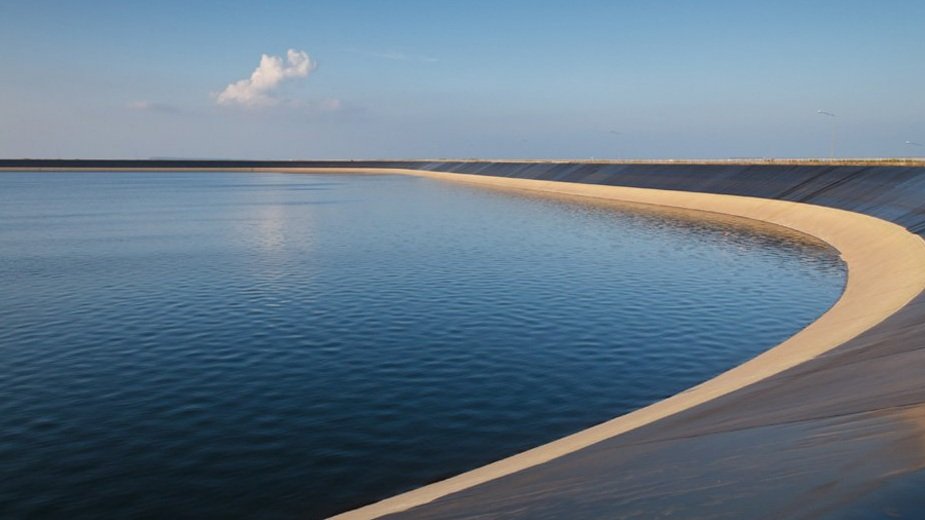
Balmoral Water Storage Facility
Water storage will provide reliability to enable farmers to meet the challenges of climate change and increased environmental flows in the Hurunui and Waiau Rivers. A new up to 10Mm3 storage pond is proposed, fed from the Hurunui River via the Balmoral scheme using existing consents. Water storage will allow farmers to be more resilient in the face of climate change, future proof their farming businesses and provide certainty for continued investment in local agribusinesses and the community. High reliability of water supply is critical in allowing our farmers to diversify their land use into other high value food production in the area.
Why do we need a storage facility?
The Balmoral Scheme irrigates approximately 8,000ha of land within the Hurunui catchment and currently delivers a good level of reliability for Amuri Irrigation Company (AIC) shareholders. However, when the Hurunui-Waiau River Regional Plan (HWRRP) became operable in 2013, it introduced higher environmental flows for both the Waiau and Hurunui Rivers.
Increased minimum flows will have significant implications on AIC’s current reliability of supply and further increases are likely in the future. These will limit AIC from taking water when the river is running at lower flows and introduce greater irrigation restrictions during the season.
The Balmoral Water Storage Facility (BWSF) is intended to mitigate the loss of run-of-river reliability, by adding a major source of pumped storage. The BWSF can also supplement the Waiau Scheme. AIC has modelled the financial impact on farmers and believes that the cost of constructing the storage facility is more than offset by the value in retaining a reliable supply of water. Higher reliability creates options for future land use diversity and will be critical for farmers considering moving from pastoral farming into higher value crops. The BWSF is expected to be bulk filled predominantly during winter and the irrigation shoulder seasons (August-October and April-May annually). Water not used for irrigation during the peak season (November-March) will be used to refill the BWSF, pending availability and flow restrictions.
The tables below show the different levels of reliability of the AIC schemes under current consent conditions, HWRRP minimum flows and HWRRP minimum flows with the BWSF.
AIC SCHEMES RELIABILITY - CURRENT CONSENTS
MINIMUM FLOWS (CUBIC METRES PER SECOND)
Project Location
PROPOSED BALMORAL WATER STORAGE FACILITY SITE
PROPOSED SITE LAYOUT
What are we Planning?
We propose constructing the Balmoral Water Storage Facility on a site adjacent to Tekoa Road and the existing Balmoral irrigation race within the Balmoral Forest, approximately 19km southwest of Culverden on land owned by Ngāi Tahu Farming.
The site is located on an upper alluvial terrace in the Balmoral Forest which gently falls in a SE direction. Currently the site is partially covered in exotic pine forestry plantation and the remainder in pine slash and exotic weed vegetation. The total site area affected by the BWSF is 134ha. The storage facility embankment footprint is 92ha. Proposed dimensions for the storage facility are 800m wide by 1,100m long (surface area 0.79km2). 10Mm3 is the upper limit for size. Consents will be pursued for a 10Mm3 pond, with the final size determined with pricing from the Contractor. This decision will depend on the appetite for storage from farmers; assessments of future climate change and land use opportunities; construction and funding costs.
Specifications:
-
A 10Mm3 storage facility with associated infrastructure such as the inlet, outlet, and a flow control structure within the Balmoral irrigation race. A rectangle was considered the most efficient shape from an earthworks and lining perspective.
Depth: 13.5m (max height 15m - height varies along length)
Crest length: 3.57km rectangular perimeter, Crest width 5m
Storage volume to embankment crest: 11.3Mm3
Freeboard: 1.5m (min freeboard 0.9m) is provided between the full supply level and the dam crest.
10Mm3 is the upper limit for size. Consents will be pursued for a 10Mm3 pond, with the final size determined with pricing from the Contractor. This decision will depend on the appetite for storage from independent irrigators; assessments of future climate change and land use opportunities; construction and funding costs. This water can be made available to farmers downstream of the Pahau River confluence through a release from the pond to the Pahau River via the existing bywash structure located at the Top Pahau Rd Bridge, or via a water swap for those farmers upstream of the Pahau River confluence.
-
The structure comprises a geomembrane lined ring embankment which utilises material (sandy gravels, cobbles and boulders) sub-excavated from the floor of the BWSF to construct a perimeter embankment dam.
The preliminary design includes a synthetic liner (likely geomembrane (HDPE, LLDPE, PVC) with the final selection made at detailed design stage.
-
2m3/s water will be pumped from the existing Balmoral irrigation race into the BWSF over the embankment through a 1200mm HDPE pipe into concrete chute via an inlet structure. A concrete channel with energy dissipation is installed in the reservoir to reduce erosion potential.
-
5m3/s water is returned to the Balmoral irrigation race through a 2100mm concrete pipe via an outlet structure and control gate that will control the outflow. This gate acts as a hydraulic isolation to the outlet structure for the safe containment and control of the storage and a spillway which can control water levels or dewater in an emergency. A network of subsoil drainage pipes discharging to soak holes are located beneath the BWSF for leak detection beneath the geomembrane liner and to control seepage and water table mounding.
Investigations
The design has considered a wide variety of factors.
-
The site is in a seismically active region and seismic resilience is an important design consideration. The closest active fault is the Hurunui Peak Fault located 1km north of site. We have completed extensive geotechnical investigations and seismic analysis and drawn the following conclusions:
There is no evidence of active fault surface rupture deformation at the site.
The site is not at risk of secondary fault rupture from the Waitohi Downs Fault.
Based on inferred terrace aging, there is not any evidence of any 1 in 10,000-year active fault surface deformation. This has been confirmed by OSL testing.
Initial investigations of active faults in the area by GNS Science identified two possible faults east of the Waitohi Downs Fault, which are the closest fault-like features to the pond site. Further seismic investigations (test pitting, ground penetrating radar and shear wave reflection profiles) concluded that these features were more likely caused by erosion and pose no tectonic surface fault rupture threat to the pond site.
All known faults at or near the site with a recurrence interval of less than 120,000 years have been considered in the fault hazard assessment and seismic hazard analysis.
-
The site is known to experience frequent high winds. This hazard has been considered in assessing wave run up on embankment slopes, freeboard, and the uplift of geomembrane liner.
-
The risk of surface flooding inundating the site is considered low as the site is elevated above the Hurunui River flood plain, although flood control facilities have been considered based on hydrological studies. There is no external contributing catchment to the BWSF and only rain falling on the reservoir can generate flooding.
-
The area has very low liquification potential.
-
The site does not indicate land instability features.
-
The flat terrace separating the site from alluvial fans provides good protection against future erosion.
-
Not considered an issue and estimated to be located at 6-20m below ground level (average 15mbgl).
-
We will monitor bird numbers and take action if there are problem congregations. No hunting will be permitted on the pond to protect the pond liner.
-
The pond is located on private land with access secured by an easement. The easement does not provide for recreational use as the pond is a working piece of infrastructure with a very expensive liner, fluctuating water levels and operating pumps and an outfall.
AIC does not currently allow any scheme ponds to be used for recreational activities due to health and safety risks. This approach is consistent with management of other large water storage ponds in Canterbury.
-
AIC is pursuing 35yr operating consents and 10yr construction consents. This takes into account the estimated construction time of four years . AIC already holds resource consents to take, store, use and discharge water over an area of land on the northern side of the Hurunui River at a rate of 5.258m3/s.
The BWSF will not require the abstraction of water above the already consented rates or volumes.
LIDAR HILLSHADE MAP WITH ACTIVE FAULTS AND ‘POSSIBLE’ FAULTS (BOTH SHOWN AS RED LINES) MAPPED BY LITCHFIELD ET AL (2017)
POSSIBLE ANCIENT LANDSLIDE FEATURE AND ALLUVIAL FAN DEPOSITS
Indicative Project Programme
-
2023-2025 >
Drafted and submitted Resource Consent applications to Environment Canterbury. Engaged with Stakeholders.
-
Mid 2025 >
Resource Consent publicly notified.
-
Late 2025 >
Detailed Design complete. Construction documents to Contractor for pricing. Consents issued.
-
Mid-2026 >
Award Construction Contract.
-
Mid-2026 >
Commence Construction.
-
Early 2029 >
Construction Complete. Storage facilities filled and commissioned.
Effects during Construction
Construction of the BWSF will take place over a long period of time. We have considered how construction work may affect neighbouring properties. A Construction Management Plan (CMP) will be prepared which will outline the controls we intend to put in place to mitigate any impact from factors such as traffic movements, dust, noise and the visual impact.
-
The following mitigation measures are proposed to reduce and minimise the traffic effects associated with the BWSF:
Location of the access road in a practical location to minimise traffic nuisance;
Traffic movements using the public road network will be scheduled to occur during ‘business hours’ (6am to 7pm Monday to Saturday) where practicable, and;
The provision of sufficient parking within the Construction Site (‘Site’) to ensure that vehicles do not idle on roadsides.
With all these measures in place, any traffic effects associated with the BWSF can be managed in a manner that is appropriate to the roads that service the Site.
The potential plant equipment required on site for construction of the BWSF is currently estimated as follows:
Scrapers and/or Dump Trucks: 10-25
Dozers and/or Excavator: 5-10
Graders: 3-5
Water Cart: 5
Vibrating Roller Compactor: 5Combined Total Plant: 28-50
The material quantities required for construction, with potential vehicle movement and estimate duration is currently estimated as follows:
Cut-to-fill Earthworks: 2,123,800m3 - within site - 20-36 months
Water Cart: 960,000m3 - within site - 36 months
Rock Riprap: 140m3 - 30 one way - 12-24 months
Concrete Delivery: 500m3 - 70 one way - 12-24 months
Fuel Delivery: 1,800,000 litres - 180 one way - 3 years
Liner Delivery: 811,968m2 - 120 one way - 18-36 months
Workforce Transport: 30 vehicles per day - 90,000 - 3 years
Miscellaneous Visits: 3 vehicles per day - 9,000 - 3 years -
the BWSF over a long period of time, minimising dust is an effect which will be incorporated into day to day processes for the contractor.
There are no sensitive areas near the BWSF Site and only one dwelling within a 1km radius of the Site. We will manage construction activities so any effects on this dwelling are minimised as far as practicable.
Mitigations
The preliminary CMP includes the following dust mitigation measures:
Limit Site traffic speed to a level to reduce the production of dust into the atmosphere.
Stabilised entrance at the entry/exit points of the Site with provision of a wheel wash facility.
Wet suppression via water trucks and/or the inclusion of polymers can assist with stabilising accessways if required.
Phasing of earthworks to isolate and/or reduce the area of exposed earthworks, including limiting earthwork activities in specific areas during periods of high wind.
Minimise drop heights when loading and unloading vehicles.
Limiting stockpile heights and sheltering them if necessary.
Placement of mulch or granular fill over exposed surfaces as soon as practical.
Stockpiled material has the potential to create dust nuisance. These areas will be stabilised as soon as practical, and stockpile areas will be managed to reduce the potential for dust.
The following mitigation methods are proposed to control dust from stockpiles:
Protection or covered storage in sensitive locations.
Reduced/controlling stockpile height and slopes (reduce wind entrainment).
In the extreme event that remedial measures are found to be ineffective for the control of dust, works may be suspended as a precautionary measure until conditions are suitable for resumption.
Stabilisation of stockpile areas away from the Site boundary.
-
Due to the number of vehicles on Site, noise disturbance has also been considered as part of the CMP.
There is one dwelling located to the south of the Site, on the lower terrace approximately 350m away and all other dwellings are located north, east and west on the upper terrace above the Site at distances greater than 1.3km away.
The following mitigation measures are proposed to minimise noise effects associated with the construction of the BWSF:
An AIC representative will be available to respond to any noise complaints should they arise, with a procedure implemented to address complaints accordingly. The contact details for this person will be made available on the sign at the Site entrance.
Works will be limited to between 6am to 7pm Monday to Saturday. No work will be undertaken on Sundays or public holidays.
-
The BWSF Site is tightly enclosed by pine forestry next to Tekoa Road that extends through to McKays Road and the rising landforms of Tekoa range. Any views to the BWSF are likely to be confined to motorists, local farmers and workers, and forestry workers along Tekoa Road, and the farms directly north of the Site. Next to Tekoa Road, native revegetation is proposed across the stockpile and soil disposal areas, storage compound and truck turning area to minimise any visual impact from the Site.
BALMORAL WATER STORAGE FACILITY SITE
PINE BUFFER AND NATIVE VEGETATION TO BE REINSTATED
Dam Break Assessment
Large dams, like other pieces of major infrastructure (such as buildings and bridges) are designed on the basis that the higher the consequences of failure, the higher the design standards and performance requirements for the structure. The BWSF’s design, performance, construction and operational safety assurance criteria must be undertaken in accordance with the NZ Dam Safety Guidelines (2015).
-
These guidelines require a dam break flood hazard and consequence assessment to be completed. This assesses the consequences of an uncontrolled release of the pond’s contents via a dam failure and establishes the criteria for which dam design, construction and operational safety assurance are based.
This work was undertaken by Riley Consultants and is a standard tool used across the industry. This classified the BWSF as a High Potential Impact Classification (PIC). Earlier modelling of smaller dam options were also classed High PIC and this classification is considered appropriate for preliminary design. A High PIC classification also requires the investigation, design and construction to be peer reviewed, and we have involved a peer reviewer since the early stages of this project.
Identifying potential scenarios is an important step in the design process as it allows for improved understanding of the processes leading up to a dam safety incident or failure and therefore what mitigation or defensive measures should be incorporated into the design to prevent or reduce their likelihood or severity.
As the BWSF has no contributing catchment and is not at direct flooding risk from the Hurunui River, potential failures occurring during wet weather conditions are not expected and the modelling was based on sunny day conditions when the BWSF is most likely to be at capacity.
The assessment looked at the worst-case scenarios in terms of population at risk and combined damage levels, which was a piping type failure of the eastern embankment. At this location, the embankment is near its highest, and any dam break flood wave would be directed over land for a considerable distance before entering the Hurunui River.
Using a computer model developed from a hydraulic modelling tool, a large portion of water would be directed east and north and not directly south-east into the Hurunui River. The resulting water depths were estimated across the plains and the Hurunui River using the hydraulic model so that the damage and population at risk could be estimated. Riley also advise that vehicles travelling SH7 are at risk should a breach occur.
Modelling of alternative breach locations along the northern, western and southern embankments indicate a broader envelope of hazard, but with similar or slightly less consequences. A breach on the southern or western embankments would result in a larger proportion of water flow into the Hurunui River, and less on the floodplain. Damage or destruction to downstream properties may still occur, however the velocity of water inundating SH7 would be lower, and the flow within the Hurunui River of up to 1300m3/s comparable to a 1 in 500-year annual exceedance probability (‘AEP’) flood event.
If a breach were to occur on the northern embankment, Riley advises that the maximum breach height would be reduced by at least 5m, with a lower volume of water released from the breach. The depth and velocity of water inundating SH7 would be similar to the modelled critical breach location, and the inundated stretch of road would be the same, if not slightly shorter, when compared to the selected breach.
-
The most likely Potential Failure Modes (PFMs) associated with this type of structure are:
Liner failure
Extreme seismic ground shaking causing deformation
Separation at the interface with the main conduit or other concrete structures
High winds generating large wave runups on the upstream slope causing overtopping of the embankment
Erosion damage of the spillway chute, main conduit, or energy dissipators
The design process will address all relevant failure modes in greater detail and implement measures as necessary to mitigate the associated risks.
-
In response to the BWSF’s high PIC rating, plans and systems must mitigate the identified risks associated with the BWSF and ongoing operations will need to comply with a dam safety management system to ensure its continued safe operation.
The following measures are proposed for safety management:
A Dam Safety Management System (‘DSMS’): This system provides AIC with a timetable to complete dam safety management activities. It also provides a risk-based decision-making framework for addressing dam safety issues should they arise. To implement the DSMS, a network of instruments, deformation survey marks and visual inspection points will be installed during construction to allow for performance monitoring once operational. Design of the network will be undertaken during the detailed design phase to allow for modification during construction, as necessary. The system will be robust and be able to be monitored by non-specialist personnel within AIC.
An Emergency Action Plan (‘EAP’): The EAP’s purpose is to minimise the potential for negative effects by implementing both preventative and emergency actions should a potential safety emergency arise. If failure cannot be prevented, the purpose of the EAP is to limit the effects of the failure on people, property, and the environment downstream of the BWSF.
Safety Inspection Schedule: In addition to the regular safety management procedures undertaken by AIC, a dam safety inspection by a suitably qualified and experienced dam engineer will be undertaken annually. A comprehensive dam safety review by an independent and suitably qualified expect will be undertaken every five years. The proposed safety inspection and review are consistent with recommendations in the New Zealand Society on Large Dams (NZSOLD) guidelines.
Who can I contact about this Project?
-
Sara Black
PROJECT LEAD
021 710 721